How to choose the refractory material for the rolling heating furnace?
- rsrefractorybrick
- Jul 19, 2022
- 2 min read
Steel rolling heating furnaces are often used as thermal equipment for heating billets or small ingots and are mainly composed of a furnace roof, furnace wall, and furnace bottom. The long-term working temperature is lower than 1400℃. For continuous or annular heating furnaces, the furnace temperature of each part can be divided into three sections: low, medium, and high temperature. So, how to choose the refractory material of the rolling reheating furnace?
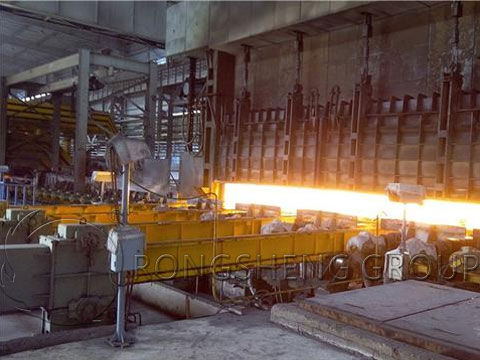
The main reason for the damage of the furnace lining is the deformation and peeling of the furnace lining caused by temperature fluctuations caused by intermittent operation and furnace shut down. The main reason for the damage to the bottom of the furnace and the root of the furnace wall is the chemical reaction between the molten iron oxide slag and the bricks.
According to the working conditions of the heating furnace, the appropriate refractory materials should be selected according to the conditions of different parts. Only by achieving a reasonable configuration of materials can the lining materials of the heating furnace be long-lived and energy-saving. So, how to choose the refractory material of the rolling reheating furnace?
After nearly 30 years of development, refractory materials for heating furnaces are now generally built with refractory castables + anchor bricks. Simple construction, easy operation and low engineering cost. It is a good material for industrial kiln construction.
01 Low-temperature section
The low-temperature section is also called the preheating zone of the rolling heating furnace, and its working temperature is generally below 1200 °C. The use of high alumina mud castables with an Al2O3 content of about 50-55% can fully meet the needs of use, or light castables can be used as the furnace lining. It can reduce the surface temperature of the furnace wall, so as to save energy and reduce consumption.
02 Medium and high-temperature section
The high-temperature section is also called the heating section and soaking section of the rolling heating furnace, and its working temperature is generally around 1200-1350 °C. A low cement castable with an Al2O3 content of about 60% can be selected. The raw material of the castable should be a raw material with low impurity content, which can improve the performance of the castable at about 1350 °C.
The work lining castables need to choose a masonry method combined with anchor bricks. The anchoring bricks can be high-alumina anchoring bricks of the national standard LZ-55.
Contact us for free samples of rolling furnace refractories in Kenya.
Comments