Electric Furnace Bottom and Furnace Wall Refractory Materials Magnesia Brick
- rsrefractorybrick
- Jun 20, 2022
- 3 min read
The electric arc furnace is a device that uses the arc generated between the electrode end and the charge as heat energy to make steel. The electric arc furnace consists of the furnace top, furnace wall, furnace bottom, and tapping groove. Electric Furnace Bottom and Furnace Wall Refractory Materials Magnesia Brick.
Electric Arc Furnace Wall Refractory Materials
The furnace wall of the electric arc furnace is divided into the general furnace wall, the slag line area, and the hot spot near the arc. Generally, the furnace walls are mainly built with magnesia bricks, dolomite bricks, and periclase bricks. There are also unburned magnesia alkaline bricks and asphalt combined with magnesia and dolomite ramming materials. The walls of electric arc furnaces for ultra-high power or smelting special steel are built with magnesia-chrome bricks and high-quality magnesia bricks.
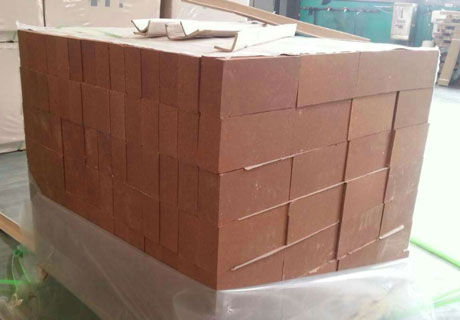
The slag line area and the hot spot are the weak links of the furnace wall. Since the life of the furnace wall mainly depends on the damage degree of the hot spot, special attention should be paid to the furnace lining of this part. In the early days, magnesia-chrome bricks were mostly used for masonry, and the service life was 100-250 heats. Now magnesia-carbon bricks are widely used in masonry, which can show excellent high-temperature resistance and slag resistance. The service life is significantly improved, reaching more than 300 heats.
In order to balance the damage to the furnace wall and prolong the service life, the furnace wall also adopts the measures of an inlaid water cooling box or water cooling jacket. Spray a layer of refractory paint on its inner surface to make the slag form a protective layer. It can effectively reduce the unit consumption of refractory materials, but the corresponding energy consumption has increased.
Refractory Materials for Electric Furnace Bottom
The bottom of the furnace and the slope of the embankment form a melting pool, which is the part where the charge and molten steel are gathered. When the lining of the furnace bottom reacts with slag and iron oxide to form a metamorphic layer, it can also become loose due to the reduction of some components during the reduction period, often causing floating due to the intrusion of molten steel. Therefore, the masonry or knotted lining of this part should have the advantages of uniform overall performance, tight masonry, good high-temperature performance, high strength, corrosion resistance, erosion resistance, thermal shock resistance, and volume stability.
Use good magnesia or fused magnesia for the knotted lining, pay attention to the connection and occlusion of each layer during construction, and strive to be consistent in the thickness and density of each layer. There is a working layer and a permanent lining under the ramming layer. The working layer is built with tar asphalt combined with magnesia bricks, and the permanent lining is mostly built with magnesia bricks. At the slag line on the upper part of the embankment slope, due to the serious erosion of slag, lining bricks that are the same as or similar to the hot spots of the furnace wall, such as cast magnesia-chrome bricks or recombined magnesia-chrome bricks, are often used. It is better to use magnesia carbon bricks.

Refractory Materials for AC Electric Arc Furnace
In the early stage, the refractory materials for the furnace bottom of the AC arc were rammed with asphalt tar magnesia or brine magnesia to form the furnace bottom, and then more magnesia bricks and low-grade magnesia-carbon bricks were used to build the furnace bottom. By the 1990s, my country began to use the magnesium-calcium-iron dry vibration ramming material at the bottom of the furnace. Metallurgical spare parts are simple and convenient to construct, do not need to be baked, and can be directly used for steelmaking after construction. The material is magnesium calcium iron dry vibrating ramming material. Using the low melting point calcium ferrite it contains, when the temperature rises above 1000 ℃, it can quickly sinter to produce strength. Under the hydraulic pressure of molten steel, it can rapidly sinter and shrink, and its shrinkage can reach 4%-5%. It has particularly good corrosion resistance and good performance.
The general refractory materials for the furnace wall of small electric arc furnaces mainly use asphalt magnesia bricks, magnesia carbon bricks, and magnesia sand to make up the charge. For ultra-high-power large electric furnaces, high-quality magnesia-carbon bricks are used for electric furnace walls, especially high-quality magnesia-carbon bricks with very high performance for slag lines and hot spots. The furnace wall repairs mainly use magnesia gunning materials. Its function is to keep warm and protect the environment to prevent dust from escaping.
Electric arc furnace steelmaking requires not only a suitable refractory lining but also a high-quality conductive graphite electrode material. High-quality refractory lining materials can not only improve the furnace age of electric furnace steelmaking but also improve the quality of tapping in electric furnace steelmaking. High-quality refractory magnesia bricks for the bottom and wall of electric furnaces, high-quality magnesia bricks, looking for refractory manufacturers factory.
Comments